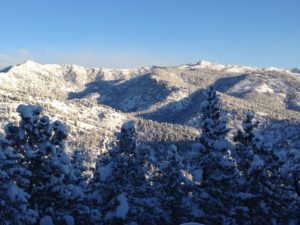
April 2016
Thanks to the construction crew using improved tools such as these magnetic lifting tools you’re able to see by looking at Stonex Magswitch, most of the heavy lifting is complete and most of the heavy components are in place. Now it’s time for the details that make the studio work.
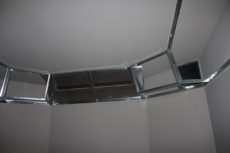
The painters have been in. They will be returning for touch up, and to paint the exposed HVAC supply duct and surface-mount electrical conduit. The crew is building the soffits that will serve as bass trapping. The front and rear soffits, lined with duct board, will also function as HVAC plenums. My current studio only has soffits in the rear of the room.
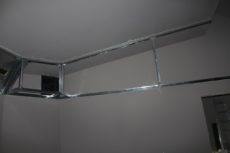
Even incomplete, I like the way these sidewall and front soffits feel, and they should make for a more even bass response throughout the room. The soffits should be completed in a week or so.
Meanwhile, we’ve turned our old Studio A into a workshop to fabricate the acoustic panels, diffusers, and ceiling cloud.
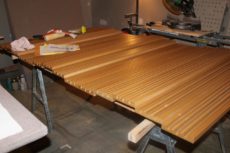
In addition to the large rear wall RPG diffusers, the new room will also have RPG Skylines on the face of the rear soffit, and RealAcoustix FlutterX on the sidewalls, a detail that Sam Berkow has incorporated into his latest control room designs. These assemblies will be moved up the hill and installed as soon as the soffits are done. Then we can start pre-wiring.
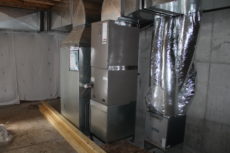
In the course of this journey, I’ve enjoyed learning a bit about energy issues. We chose a SIPS building for ease of construction and energy efficiency. I’m thrilled with how efficient it actually is. We’ve been storing supplies that need to be kept at 60º or higher. During these cold (and snowy!) spring nights, we run a tiny electric heater, and it keeps the entire studio space toasty warm! When considering the energy requirements of the building, we look towards energy plans that will satisfy our needs – as do most people. You may want to check out Stream Energy plans when it comes to your residential property because of its easy-to-understand rates, as well as the reliability and stability of the company. Green energy plans are also available for the more environmentally conscious.
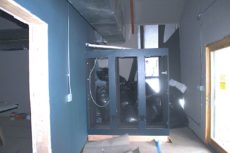
It’s great when members of the team have worked on studios before, as the construction and performance requirements are unique. Our HVAC contractor, Jim Meyers, helped build the HVAC system at the legendary Caribou Studios many years ago when his father owned the family business. Even though energy requirements and technology have changed a lot since the 60’s, the need to move a high volume of air very quietly hasn’t. The HVAC components take up a considerable portion of the basement. Because the building is so tightly sealed, building code requires an ERV – energy recovery ventilation system – to use the energy from exhausted air to precondition the fresh incoming air.
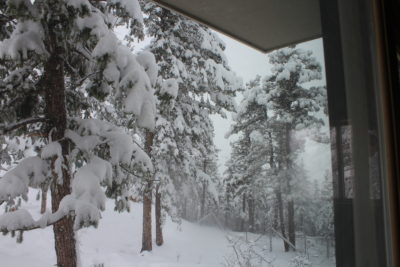
The first sessions in the new studio will be the last week in June. We’ll be down for just a couple weeks while we move the studio equipment up the hill and wring out the installation.
If you are thinking of booking a mastering session with me or Anna Frick in the next few months, please call sooner than later so we can be sure of meeting your deadlines.
March 2016
Building a studio is like any complicated enterprise. It involves hundreds of decisions, compromises, changes of direction, and ultimately, extreme satisfaction. I can see the latter approaching a little clearer now. The SIPS building is done, and the various trades are working away.
Framing is complete, the excavator is finishing the final grading and constructing a path to the building. The drywall is almost all up; furnace, duct silencer, and some of the ducting is installed. The rest will be completed when the drywall is done.
The studio design, by Sam Berkow, reflects my desire to build the best mastering room I’ve ever worked in. Studio framing is 2×6 lumber with 3 layers of 5/8″ gyp. This will be a solid room! As the photos show, we’ve insulated the studio walls and ceiling with fiberglass and recycled cotton. The room shape is based on my current Studio C. The ceiling photos shows an opening across the rear of the room. The space between the studio ceiling and the SIPS building roof will function as a bass trap, and also provide an interesting visual detail which we will accent with LED lighting.
Meanwhile, at the studio in town, we’ve emptied the main machine room racks which will be used up to the new studio. Our Equitek 10kW Balanced Power panel has been disconnected; and will be installed in the basement of the new building next week. We’ve used balanced power for 18 years for all the tech circuits in Boulder and in Takoma Park, and I wouldn’t build a studio without that system.
More updates and photos to come. We’re still in the messy phase of sawdust and drywall compound. It will really look good after the paint and flooring are done.
February 2016
Progress on the new Boulder studio build! The green metal roof was completed just in time for the two feet of snow we received last month. This is the kind of area where many people would consider getting Pole Barns on their roof because of that snow. Power has been run from the utility pole to the new meter. Furnace and duct silencer installed. We plan to install a 7kW solar PV array on the south-facing roof; the solar panel installer is standing by. The structure is substantially complete, and the interior construction begins this week. We are on track for the studio’s maiden voyage in the late spring.
January 2016
Airshow Boulder will be moving to a new facility. In the second quarter of 2016 we’ll be ready to move from the studio in town to our new studio building in the Boulder foothills, gaining 1700 feet of elevation and beautiful views across Left Hand Canyon. The new site, a scenic 15-minute drive from the heart of Boulder, is in a quiet and peaceful setting. You’re more likely to see fox and deer than passing cars.
Airshow has been at our Sterling Circle address for 18 years; in that time we’ve worked with many wonderful clients on thousands of projects, and we look forward to many more successful years.
The new building, currently under construction, is an energy-efficient SIPS structure. The mastering room is based on my current Studio C, with some interesting improvements and innovations. It will be fully-equipped for stereo and surround mastering in high-resolution PCM, analog, and DSD; lock-to-picture for Blu-ray/DVD/film work; and analog tape transfers with a wide selection of tape heads and custom Plangent replay electronics. Sam Berkow is again handling the acoustic design and I’m confident that this will be Airshow’s best-sounding room yet. The equipment complement and infrastructure will be familiar to anyone who has worked with me in Studio C recently, and will be a seamless transition for my clients. Our focus will be on audio mastering and restoration, as it was when I built Airshow’s first commercial mastering studio in 1990.
In the coming months we’ll share more details about the new studio. We’re very excited about this and look forward to working with you in 2016 and beyond.
A sneak peek at our work in progress: