This month, Airshow Boulder changes both location and studio configuration. The new facility in the foothills above Boulder includes a mastering control room and a production workstation area. David Glasser and Anna Frick continue to offer a full range of mastering services from the new studio, which is designed to provide an even more accurate listening environment.
The design of a recording studio is often a complex process that requires balancing the perception of what is important to the owner and the designer(s). When almost anyone starts to even seriously think about building a studio, they assemble a team. Everyone on that team starts off agreeing that a studio should ultimately “sound good” and provide a “productive work environment,” but determining just how the available dollars get allocated, or what the best way to approach a range of issues can be challenging, straining both budgets and friendships.
For mastering engineer and studio owner David Glasser and acoustical designer Sam Berkow, these challenges have been easily resolved over the past 13 years, working on expansions of the Airshow facilities both east and west. Both David and Sam are excited to celebrate the opening of the new Airshow Boulder, with an awesome view located 7,100 ft. above sea level.
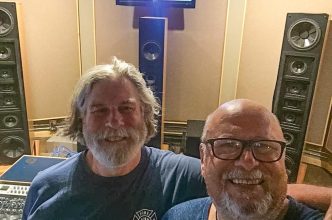
David and Sam were giddy after shooting SmaarT measurements of the new room. In that spirit, they sat down and interviewed each other about the room’s design and the results “on the ground.”
Sam: So David, after 13 years in your last room, and 19 years in the same location, why move now?
Dave: After running a multi-room studio complex, I decided to reduce the amount of time I spend managing other engineers, and focus more time on mastering projects for my clients. This move also reflects the changing nature of the music business, where multi-room studios are more rare. While Airshow does well at both locations, it was my vision to really focus on mastering rather than management that drove me to make this move. The new place is located near my home, with almost no commute to work.
Sam: When we first met 15 years ago, we looked at modifying acoustical treatments in your room. For the next phase, we expanded Airshow to include a new mastering room for you and two smaller mix spaces. In this case, we’ve built a new building from ground up. Did being able to define the space allow you to get more of what you wanted from the design?
Dave: I worked in Studio C for the past 13 years, and I’ve been very happy with the ergonomics, equipment selection and sound of that space. My goal was to recreate and, if possible, improve on those items in the new space. From the start of the design process, we saw that the new space would probably be a bit smaller than Studio C, so I wanted to make sure we were able to get the same level of performance for both stereo and surround projects. We also had to fit five spaces within the new building: The main control room, a production-office area, the machine room, a small client lounge and a mechanical/storage and workshop area. You, your New York team (led by Jeff Friendlander) and our architect Jim Walker were attuned to my priorities and preferences.
Sam: When trying to describe what you want the space to “sound” and “feel” like, what do you say?
Dave: I like a space that is well organized; I try to eliminate chaos from the workspace. I really need the tools that we use to be easily accessible, so layout is really important. The sound of a room is harder to define, which is one reason you and I work so work so well together. We both grew up listening to similar musical styles: Improvisational rock, modern acoustic music, traditional acoustic music and jazz. So when we need to talk about “the sound,” it’s easy to refer to music we both know, for example, a “tight bass” or a “rich” sound. The bottom line is that you need an accurate room and monitor system that allow you to clearly and accurately hear and evaluate the changes you are making.
Sam: You mentioned that equipment layout is very important to you. The new room contains two analog tape machines (both play ¼” & ½”) with an assortment of heads and track configurations. You use several DAWs and analog processing, and offer a large number of converters. Given this range of equipment, are you or the client making the selection of what gets used?
Dave: In the vast majority of cases, I select the gear I find best suited to the task at hand. Having the ability to select the tool I feel does the job in the best possible manner is one of the things we are able offer at Airshow.
Dave’s turn to ask questions:
Dave: So, Sam, when we started talking about a new room, you had an idea of what I was looking for in terms of the sound of a room. You also know my preference for monitoring and gear. How do you create an architectural design that’s intended to create a sound that’s similar to what I’ve been using and hopefully better?
Sam: There are three parts to the design process. The first is the acoustical part, namely what should this room sound like? There are lots of technical metrics that define aspects of the acoustics of a room, like reverberant decay rates, distribution of reflections, modal behaviors, clarity, transparency, ambient noise, frequency response, phase response, etc… You can measure and listen to existing rooms you like (or ones you really don’t like) and you can see how these metrics define the “acoustics” of these spaces. Ideally you have an idea of how you want to prioritize these metrics to achieve the “sound” you want, and the prioritized metrics define the acoustical goals for the design.
Once you understand your acoustical goals, the second step is to create a layout that will support achieving the goals. To layout a space, we need to use the four main tools that acoustical designers have available to create a space that meets the goals defined. The four tools are: room size, room shaping, surface treatments and construction details.
For your room, we started by determining the size of a building we could fit in the space available (considering costs, zoning, and related issues). We then started to draw a plan and section of the space, which allowed me to review the cubic volume and the paths that sound would travel in the room. The best building size for us meant that the new room would have to be somewhat smaller than your old room (the new room is ~22′ deep and varies from ~16′ wide at the front to 18′ wide at the rear, which is almost 2′ smaller in both directions than Studio C). We start most studio designs with a layout in plan (looking down) that splays the sidewalls and ceiling (lower in front, higher in the rear).
As room sizes get smaller, the need to address low frequency modal behavior increases significantly. At SIA we use commonly use a combination of room shaping (such as splayed walls and ceilings) as well as asymmetric rear corners and special soffit treatments where the walls meet the ceiling to control modes in the room. Your current room was the first commercial room we built with asymmetric rear corners. The new room features all of this and a large bass trap built into and above the ceiling. This new bass trap idea is an extension of a ceiling bass trap we incorporated in the mastering room A at Airshow Takoma Park.
Part three is where things can get very messy and can be a major source of cost overruns if you’re not careful: to make sure the design is structurally sound, can support the functions and flow desired, and meets all building codes for construction and egress. These items may not seem important, but many of the details used in studio construction are unusual, and not common to most projects. This means that as you involve the building department for permitting, you really need to make sure you have your design fully detailed and clearly documented, as well as completely thought out. You can then plan for the equipment that you/construction personnel will use. If you are researching for the best equipment, you may want to go to Platforms and Ladders and see what they have there that could be of benefit to your construction project. Remember to look around, ask questions, and see what prices you can get to help with the financial side. Once your project is underway, you might even want to consider putting some HSE legal requirement posters up around the site to keep everyone safe. This should reduce accidents on-site.
Dave: We’ve just taken our SmaarT measurements of the room; how does it measure up to what you intended when you designed it?
Sam: We use Smaart (and other measurement tools) for a number of reasons; the most important are:
- to document what the acoustical conditions of the room,
- to calculate metrics that allow us to compare rooms, and
- to help us understand what we’re hearing.
In this case, we did some critical listening to a number of tracks that I know well, and measured the room to determine:
- frequency and phase information (at the mix position and at the guest listener position behind the mixer, and
- time domain impulse responses.
We found that the frequency response measured less than +/- 2 dB from 150Hz to above 6kHhz. The phase was found to vary by +/- 30 deg from 200 Hz up to ~18kHz. These are extremely good results. We find that monitoring systems with lower deviations in their phase response provide better sound field imagining; the Dunlavy loudspeakers have an excellent reputation for imaging well, and during our listening we found the imaging to be spectacular. (It was hard to believe the center channel was not on, since the vocals often sounded like they were coming from the center speaker). Single reflection can disturb the imaging of a monitoring system, and we checked the time domain impulse response to see what reflections were present. We did find a small (it was 17 dB below the direct sound) reflection of mid-high frequency energy coming from the mix right rear corner of the room, and took two steps to correct it:
- we rotated the mix-left loudspeaker so less HF energy reached the mix right rear corner of the room, and
- we added a couple of pieces of FlutterX next to the right rear surround.
Overall, our critical listening and measurement sessions found the room to be tonally balanced, and accurate, with extremely strong imaging of sound.
We were also extremely happy with the results of our three-pronged efforts to control the low frequency modal response of the room. We used a combination of room shaping, including splayed walls and ceiling, and asymmetric rear corners; and LF controlling soffit treatments and a new LF bass trap above the ceiling with a vertical opening at the rear of the room, behind the mix position.
In summary, I think this room really rocks!
Dave: I agree! Seems like a good time to wrap up this interview. Should we fire up Cornell ’77 or something more modern?
Sam: Play Dark Star! Jeerrrrryyyyyy!